Hot rolling and cold rolling are both processes for forming steel plates or profiles, and they have a great influence on the structure and properties of steel.
Steel rolling is mainly hot rolling, and cold rolling is usually only used to produce small-sized steel and thin plates with precise dimensions.
Common steel hot and cold rolling situations:
- Good corrosion resistance: The base material and surface coating of the plate have strong corrosion resistance. The high-strength magnesium-aluminum-zinc alloy is used as the coating, and its corrosion resistance far exceeds that of traditional steel plate materials.
- High strength: Aluminum-magnesium-zinc plate has excellent resistance to strong winds, earthquakes, and heavy pressure. It is lighter than traditional steel plate materials, but has higher strength and rigidity.
- Beautiful and durable: The material and even the color of the plate are very flat, and the surface coating has excellent color stability and gloss, which greatly extends the service life.
- Safety: The plate has a very high fire rating and safety performance, which can prevent fires to a great extent.
- Convenient construction: Compared with traditional steel plate materials, aluminum-magnesium-zinc plate is lighter, convenient for construction, reduces construction period, and reduces manpower and material costs.


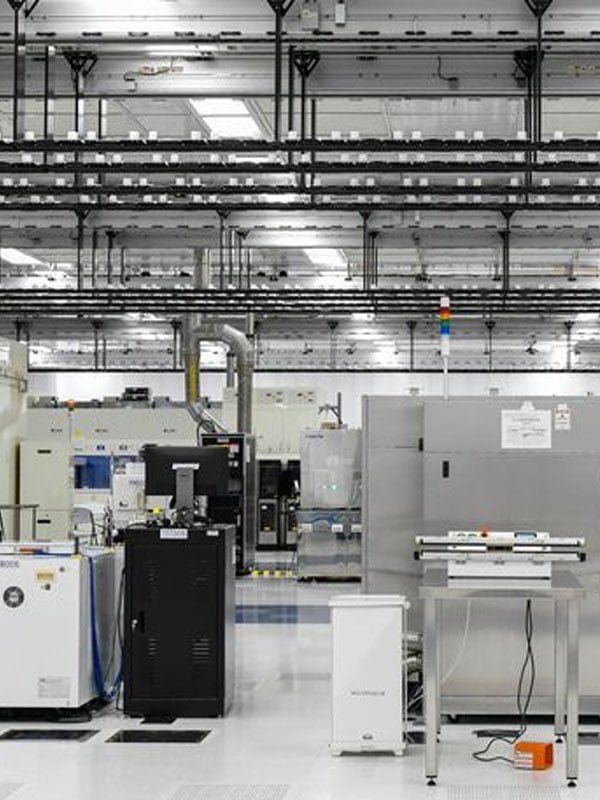
Hot Rolling
By definition, steel ingots or billets are difficult to deform and process at room temperature. They are generally heated to 1100-1250℃ for rolling. This rolling process is called hot rolling.
The end temperature of hot rolling is generally 800-900℃, and then they are generally cooled in the air, so the hot rolling state is equivalent to normalizing.
Most steel products are rolled by hot rolling. Due to the high temperature, a layer of iron oxide scale is formed on the surface of the steel delivered in the hot-rolled state, so it has a certain corrosion resistance and can be stored in the open air.
However, this layer of iron oxide scale also makes the surface of hot-rolled steel rough and the size fluctuates greatly. Therefore, steel products with smooth surface, precise size and good mechanical properties should be produced by cold rolling with hot-rolled semi-finished products or finished products as raw materials.
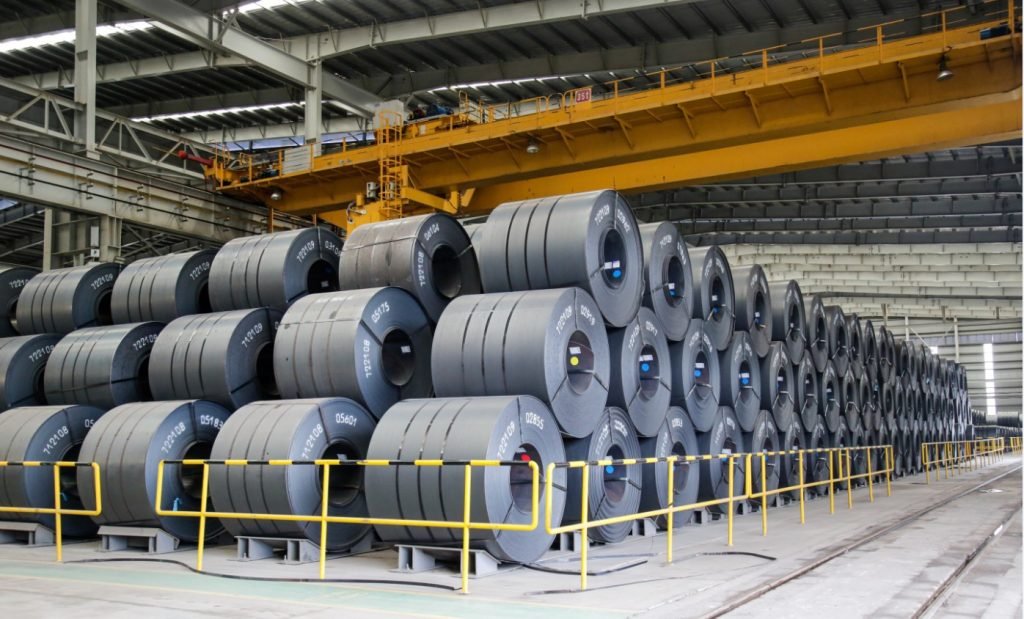
Advantages:
- Fast forming speed, high output, no damage to coating, can be made into a variety of cross-sectional forms to meet the needs of use conditions; cold rolling can cause large plastic deformation of steel, thereby increasing the yield point of steel.
shortcoming:
- Although there is no hot plastic compression during the forming process, there are still residual stresses in the cross section, which will inevitably affect the overall and local buckling characteristics of the steel;
- The cold-rolled steel section is generally an open section, which makes the free torsional stiffness of the section low. It is easy to torsion when bent and bending-torsion buckling when compressed, and the torsion resistance is poor;
- The wall thickness of the cold-rolled steel is small, and there is no thickening at the corners where the plates are connected, so the ability to withstand local concentrated loads is weak.
Cold Rolling
Cold rolling refers to a rolling method that changes the shape of steel by squeezing it with the pressure of rollers at room temperature. Although the steel plate will heat up during the process, it is still called cold rolling. Specifically, cold rolling uses hot-rolled steel coils as raw materials, and after pickling to remove the oxide scale, it is pressure-processed, and the finished product is hard-rolled coils.

Generally, cold-rolled steel, such as galvanized and color-coated steel plates, must be annealed, so the plasticity and elongation are also good, and they are widely used in the automotive, home appliances, hardware and other industries. The surface of cold-rolled plates has a certain degree of finish, and it feels smooth to the touch, which is mainly due to pickling. The surface finish of hot-rolled plates generally does not meet the requirements, so hot-rolled steel strips need to be cold-rolled. The thinnest thickness of hot-rolled steel strips is generally 1.0mm, and cold rolling can reach 0.1mm. Hot rolling is rolling above the crystallization temperature point, and cold rolling is rolling below the crystallization temperature point.
The change in the shape of steel caused by cold rolling is a continuous cold deformation. The cold work hardening caused by this process increases the strength and hardness of the hard rolled coil and reduces the toughness and plasticity indicators.
For end use, cold rolling deteriorates the stamping performance and the product is suitable for parts with simple deformation.
Advantages:
- It can destroy the casting structure of the steel ingot, refine the grains of the steel, and eliminate the defects of the microstructure, so that the steel structure is dense and the mechanical properties are improved. This improvement is mainly reflected in the rolling direction, so that the steel is no longer isotropic to a certain extent; the bubbles, cracks and looseness formed during pouring can also be welded under high temperature and pressure.
shortcoming:
- After hot rolling, the non-metallic inclusions (mainly sulfides and oxides, as well as silicates) inside the steel are pressed into thin sheets, resulting in stratification. Stratification greatly deteriorates the tensile properties of the steel along the thickness direction, and interlayer tearing may occur when the weld shrinks. The local strain induced by weld shrinkage often reaches several times the yield point strain, which is much larger than the strain caused by the load;
- Residual stress caused by uneven cooling. Residual stress is the internal self-balanced stress without external force. Hot-rolled steel sections of various cross-sections have this type of residual stress. Generally, the larger the cross-sectional size of the steel section, the greater the residual stress. Although the residual stress is self-balanced, it still has a certain impact on the performance of steel components under external forces. For example, it may have an adverse effect on deformation, stability, fatigue resistance, etc.
-
Sale
Galvanized Steel GI GL Steel Roofing Panel Galvalume Steel Coated roofing sheet
$400Compare to $600 -
Sale
12 Gauge GI Coils Cutting Sheet Thickness Metal Zinc Coated Galvanized Steel Sheets G550 Z275 Metal Steel Coil
$730Compare to $751 -
Sale
Hot dipped Ppgi Corrugated color coated GI/GL aluminum iron roll Prepainted galvanized/galvalume steel coils products
$559.99Compare to $599.99 -
Sale
Automatic zinc corrugated metal roof tile forming press ridge making sheet roofing panel iron machine for roof sheet making tile
$4,989.90Compare to $6,999 -
Sale
Chinese Manufacturer PPGL/ PPGI Steel Roof Tile Color Coated Metal Roofing Sheet Prepainted Galvanized Corrugated Sheet
$450Compare to $600 -
Sale
ASTM Light Weight Roofing Sheet SGCC,SGCH,DX51D,Waterproof and sunscreen Corrugated Steel Board Galvanized Roof Metal Sheet
$480Compare to $629 -
Sale
Rustproof Best Selling Cheap Price Customizable Zinc color coated Steel Roofing Sheet/ Pre painted Galvanized Corrugated Sheets
$399Compare to $699 -
Sale
Zincalume Zinc Aluminium Coated Roofing Sheet/ Az100 Galvalume Steel Coil /afp Antifinger Aluzinc Steel Roll
$499Compare to $599